精益制造是一种专注于最大限度地减少制造系统内浪费,同时最大限度地提高生产力的方法。浪费被视为客户认为不增加价值且不愿意支付的任何东西。精益生产的一些好处包括缩短交货时间、降低运营成本和提高产品质量。
精益生产,也称为精益生产或精益生产,是来自多个领域的组织可以实现的实践。一些使用精益的知名公司包括丰田、英特尔、约翰迪尔和耐克。该方法基于丰田生产系统,至今仍被该公司以及无数其他公司使用。使用 客户关系管理系统(CRM) 和 企业资源规划 (ERP) 的公司也可以从使用精益生产系统中受益。
精益生产基于许多特定原则,例如改善或持续改进。
精益制造是通过 1990 年出版的《改变世界的机器》引入西方世界的,该书基于麻省理工学院对丰田精益生产系统详细描述的汽车未来的研究。从那时起,精益原则深刻地影响了全世界的制造理念,以及制造业以外的行业,包括医疗保健、软件开发和服务行业。
精益生产的 5 大原则
1996年出版的一本被广泛引用的书《精益思维:在公司中消除浪费和创造财富》列出了精益的五项原则,该领域的许多人都将其作为核心原则。它们是价值,价值流,流动,拉动和完美。这些现在被用作精益实施的基础。
1. 从客户的角度识别价值。 价值是由生产者创造的,但它是由客户定义的。公司需要了解客户对其产品和服务的价值,这反过来又可以帮助他们确定客户愿意支付多少钱。
公司必须努力消除其业务流程中的浪费和成本,以便能够实现客户的最佳价格——为公司带来最高利润。
2. 映射价值流。 该原则涉及记录和分析生产特定产品或服务所需的信息或材料流,以识别浪费和改进方法。价值流图涵盖产品的整个生命周期,从原材料到处置。
公司必须检查周期的每个阶段是否存在浪费。任何不增加价值的东西都必须被淘汰。精益思想建议将供应链调整作为这项工作的一部分。
3. 创建流程。 消除功能障碍并确定缩短交货时间的方法。这有助于确保从收到订单到交付的流程顺利进行。流量对于消除浪费至关重要。精益生产依赖于防止生产过程中的中断,并实现一套协调和集成的流程,使活动不断流动。
4.建立拉动系统。 这意味着您只有在有需求时才开始新工作。精益生产使用拉动系统而不是推式系统。
推送系统用于制造资源规划 (MRP) 系统。通过推送系统,可以提前确定库存需求,并制造产品以满足该预测。然而,预测通常不准确,这可能导致库存过多和不足之间的波动,以及随后的日程安排中断和糟糕的客户服务。
与MRP相比,精益生产基于拉动系统,在有需求之前不购买或制造任何东西。拉动依赖于灵活性和沟通。
5. 通过持续的流程改进或改善来追求完美。 精益生产建立在不断追求完美的理念之上,这需要针对质量问题的根本原因,并在整个价值流中找出和消除浪费。
精益生产的8大浪费
丰田生产系统列出了七种浪费,或流程和资源,这些浪费不会为客户增加价值。这七种废物是:
- 不必要的运输;
- 库存过剩;
- 人员、设备或机械的不必要移动;
- 等待,无论是等待的人还是闲置的设备;
- 产品生产过剩;
- 过度加工或在产品上投入的时间超过客户需求,例如需要高科技机械来获得不必要的功能的设计;和
- 缺陷,需要付出努力和成本进行纠正。
虽然最初没有被纳入丰田生产系统,但许多精益从业者指出了第八种浪费:浪费未使用的人才和聪明才智。
7 种精益制造工具和概念
精益生产需要不懈地追求减少任何不能为产品增加价值的东西,即浪费。这使得作为精益生产核心的持续改进成为必须的。
精益所依赖的其他重要概念和流程包括:
- Heijunka:生产平整或平滑,旨在产生连续的生产流,以所需的速度将工作释放到工厂并避免中断。
- 5S:一套组织工作空间的做法,为工人创造高效、有效和安全的区域,并防止浪费精力和时间。5S强调组织和清洁。
- 看板:用于简化流程和创建即时交付的信号。信号可以是物理的,例如标签或空箱,也可以是通过系统以电子方式发送的。
- Jidoka:一种定义大纲的方法,用于检测异常,停止工作直到可以纠正,解决问题,然后调查根本原因。
- Andon:一种视觉辅助工具,例如闪光灯,可以提醒工人注意问题。
- Poka-yoke:一种防止人为错误的机制,例如在错过必要步骤时亮起的指示灯,在螺栓拧紧正确次数时给出的信号或阻止下一步的系统,直到完成所有先前步骤。
- 周期时间:生产零件或完成流程所需的时间。
精益与六西格玛
六西格玛是一种数据驱动的管理方法,本质上类似于精益,它旨在通过测量流程中有多少缺陷并消除它们直到缺陷尽可能少来提高质量。
精益和六西格玛都寻求消除浪费。然而,两者使用不同的方法,因为它们以不同的方式解决浪费的根本原因。
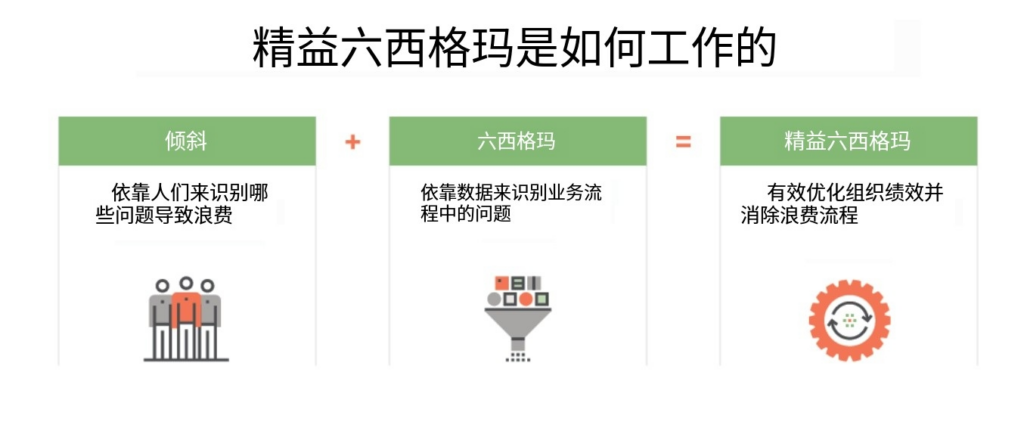
用最简单的术语来说,精益认为浪费是由客户认为不会增加价值且不会支付的额外步骤、流程和功能造成的,而六西格玛则认为浪费是由流程变化造成的。尽管如此,这两种方法是互补的,并已结合成一种数据驱动的方法,称为精益六西格玛。
- 关键词标签: 供应链和制造